Welcome to the world of:
We are Engineers and Roboholics!
In order to not lag behind Central and Western Europe - we provide you with a bit of History and knowledge
Industrial robots - the beginning of automation solutions
With the development of industry during the 20th century, the need for automation has grown. Industrial robots have started to attract more attention as a solution to overcome the shortage of labor and to meet investors’ desire for rapid expansion of productivity. Naturally, being multifunctional and flexible, robots have the advantage of being easily installed in manufacturing facilities where the placement of specialized machinery is not feasible or where comprehensive upgrades of production lines are difficult or cost-ineffective.
In addition, by collaborating with a specialized System Integrator (SI) in the implementation of robotic systems, investors can confidently navigate through all stages – from planning, budgeting, Proof of Concept (PoC), testing, installation, personnel training, to ongoing support in the years ahead.
In 2021, one of the world’s largest manufacturers launched a platform through which industrialists can easily find compatible peripheral equipment to build their desired robotic systems. Implementing robots requires connecting to peripheral equipment such as grippers, a wide range of sensors, and machine vision. This platform now allows comprehensive validation and certification of each solution in advance, even before the actual investment. As a result, it leads to a significant reduction in the costs associated with validating the entire equipment complex needed for the overall implementation.
In addition, by using the online platform, investors and their engineers accumulate a vast amount of data for subsequent learning and improvement of the efficiency of their individual robotic solution, as well as detailed insights into machine processing development. Of course, these effectiveness data are valuable not only for training other robots but also for the advancement of robotics as a whole.
Robots can be divided into two main categories – industrial robots and non-industrial robots. Industrial robots are primarily used in manufacturing, logistics, agriculture, and animal husbandry. Non-industrial robotic solutions are applied in areas such as security, medicine, healthcare, and space technologies. For example, humanoid robot Pepper and cleaning robots are included in the category of non-industrial robots.
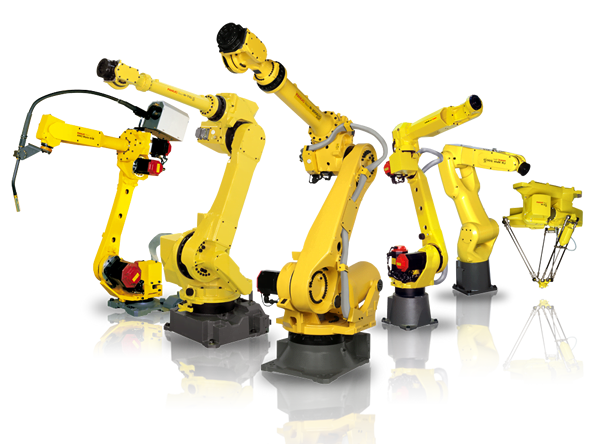
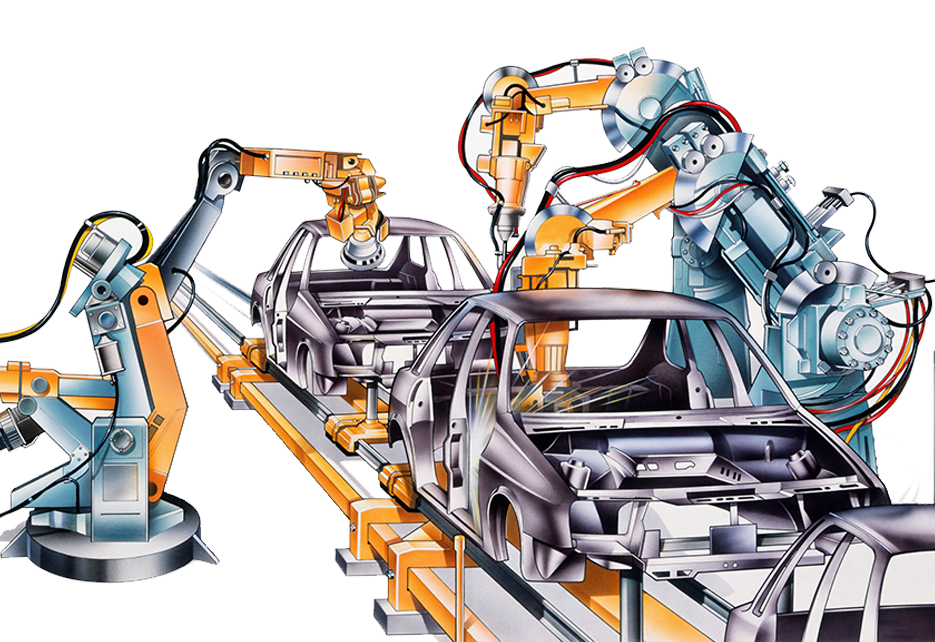
What is an industrial robot?
Indeed, the first industrial robot in the world was created and introduced in the United States in 1962. The concept of a “robot that can flexibly respond to automation through learning and playback” was presented by the American engineer George Charles Devol Jr. Devol collaborated with Joseph Frederick Engelberger, an entrepreneur who would become known as the “father of robotics,” and together, they successfully developed the first industrial robot called “Unimate” – a “colleague with universal abilities.” Unimate was a milestone in the history of robotics and played a significant role in shaping the future of automation and manufacturing processes.
Japan has been a pioneering nation in the field of robotics and automation, and it has turned robotics into a powerful trend. In the latter half of the 20th century, the development of industrial robots for Japanese industries accelerated significantly, particularly in the automotive industry. This sector showcased the capabilities of Japanese manufacturers, who had acquired high levels of expertise in electrical equipment and precision machinery. Japan rose to become a dominant global force in robotics, with its innovations and advancements shaping the industry and leading to widespread adoption of robotic technologies worldwide.
During the motorization trend in Japan, the automotive industry had particularly significant needs. For the first time, the welding process, considered difficult, dirty, and hazardous, was completely automated with robots.
Industrial robots can generally be categorized into 6 main types.
- The first type is the robot with polar coordinates. This type was widely developed in the early days of robotics. It has a centrally rotating shaft resembling a turret and an extending arm that rotates up and down.
- The second type is a robot with cylindrical coordinates, featuring a rotating shaft and an extending arm that moves vertically.
- The third type of robot operates with Cartesian coordinates and performs its movements in three dimensions, not through rotation but by sliding along its three perpendicular axes (length, width, height). This type of solution requires a larger installation area, but the mechanism is much simplified and easy to control.
- The fourth type of robot, widely used in modern times, is the vertically articulated robot. It consists of an arm with multiple joints (axes) like a human arm and a rotating shaft, and it is used in various applications such as welding, palletizing, and assembly.
- The fifth type is the Selective Compliance Assembly Robot Arm (SCARA), which includes a horizontal rotating shaft and a vertical linear shaft. It is particularly convenient for performing tasks on a worktable with a fixed height.
- The sixth and most recent type is the parallel link robot. It is highly productive and operates multiple parallel joints, enabling a combination of high-speed and precise movements.
The industrial robots and Industry 4.0
They are fast and powerful, conventional industrial robots are always installed far away from humans and with safety barriers. On the other hand, collaborative robots, the new trend in the world, draw attention because they can work alongside workers. They can be controlled in small spaces without the need for large safety barriers, allowing applications in various settings with less specialized equipment. For instance, a dual-arm collaborative SCARA robot occupies the same space as one worker. Using its two “arms,” the robot can assemble boxes, wash dishes, or package cosmetic products just like a human does. Robotic systems for automatic waste sorting in recycling facilities are also being developed, and we will soon see demonstrations of these systems in action.
Another new addition to the world of robotics is the remote collaboration systems, through which multiple robots installed far away from the operator can be remotely controlled. This innovation opens up the possibility of using robots for tasks that require human senses, which were previously considered difficult. One of the major advantages of this solution is that the robots can be directly trained for precise movements without programming. This means they can be used as a means of transferring skills, as the expertise of a skilled worker can be transferred to the robots, and later, these robots can train new workers.
The solution also supports multi-robot control, where a single operator can control several robots simultaneously. Managing multiple factories worldwide from one location using high-speed internet connectivity will present the industry with the opportunity at any given moment. This system is an ideal solution for the upcoming era of intelligent factories.
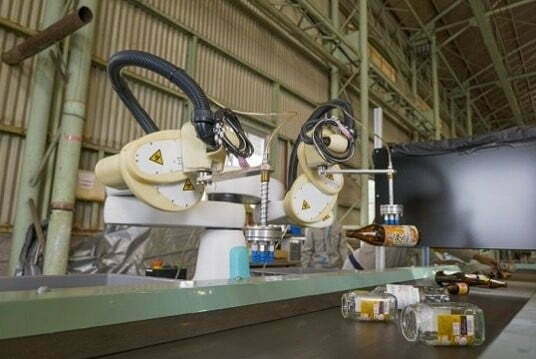
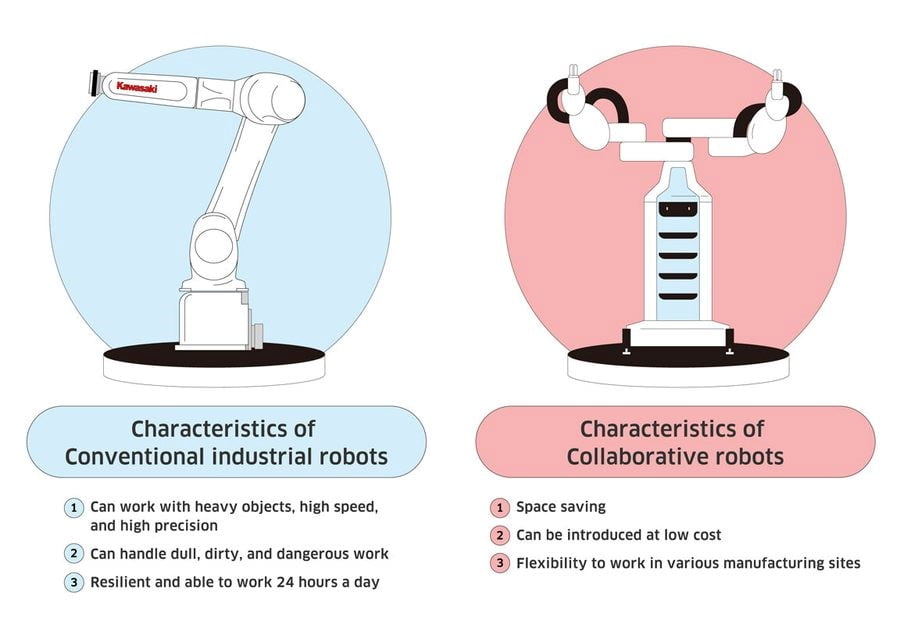
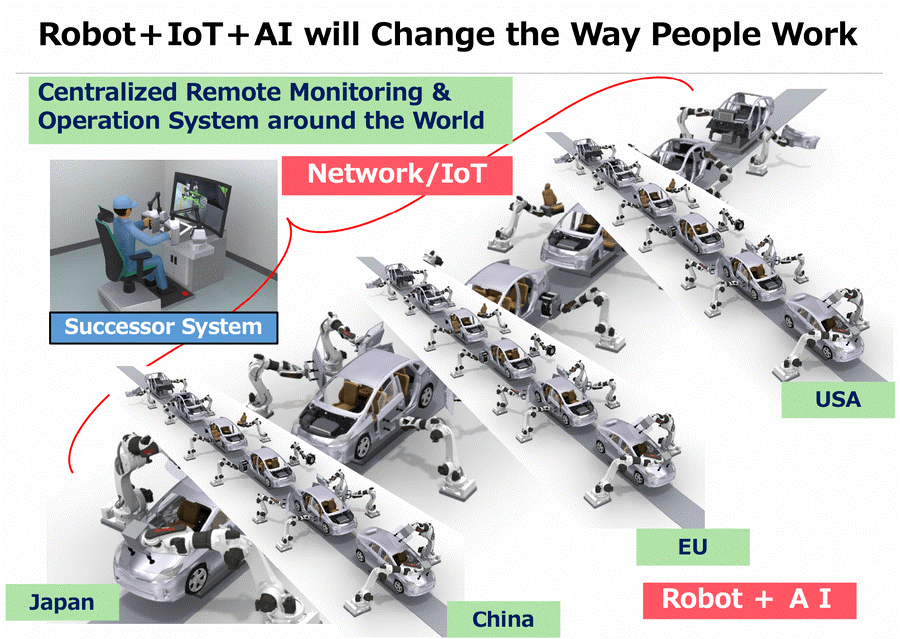